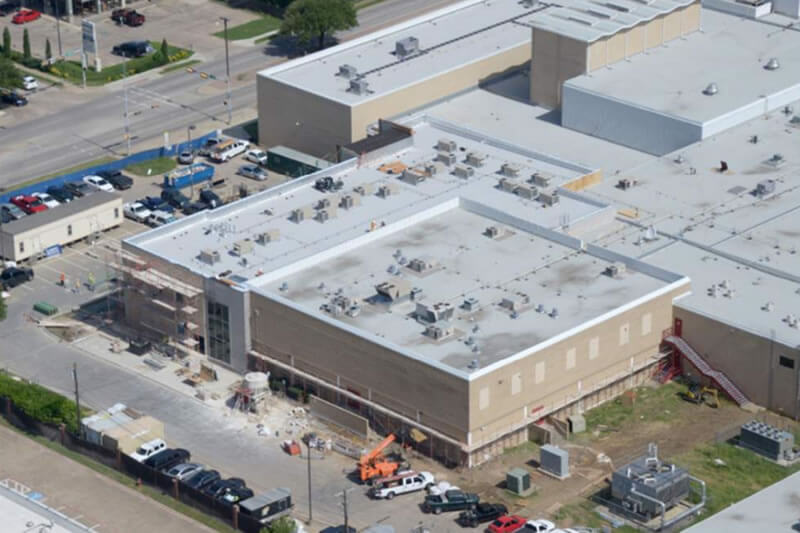
MacArthur Highschool
Project Overview
- 58000 Square Feet
- Two Floors
- The project consisted of a two-story addition to an occupied high school which the main portion had been constructed in 1963. Much of the existing school was electrically fed from an outdoor service that was specified to be replaced as soon as the regular school year was completed. This meant replacing old feeders to two existing electric rooms, a vocational shop, and the boiler room. Due to weather the overall schedule was compress by 2 ½ months and was still completed on time. Over the duration of the project the electrical contract was increased by 39% which offered its own set of challenges.
Project Narrative
The MacArthur Addition was a fairly straight forward project as far as design and functionality, what made it somewhat difficult was the loss of 10 weeks at the start of the project mostly due to weather and of course being a school, it had to complete on time. There were 32 changes over the course of this significantly
delayed 8-month project, increasing the contract value by 39%. Increasing and changing the scope of work by that amount adds a significant difficulty and burden on productivity. The main construction challenge during the project was installation of a 3000A main switchgear that replaced a tap-can which fed most of the existing school as well as the addition. We were given a 3-week window to demo and re-install 22 feeders to various parts of the school and get the new gear re-energized in order to begin finishes in the new addition.
Many of the George McKenna Best Practices were utilized during the rough in phase of the work, including a full set of install drawings and designated wall rough in products. We are also able to utilize a vender to pull all the feeders directly from the delivery truck without using any jack stands. This all improved productivity and safety.
During the course of the project we had very little rework, efficiently incorporated the changes into the workflow, effectively managed rental equipment, minimal punch list, and worked our job plan from start to finish while performing any work available to us in order to minimize crew size and long hours at the end of the project. Even with the compressed schedule only 6.5% of the labor was at an overtime rate. This resulted in a financial win in every reporting category. Shown below is the percentage of the budget used in each category:
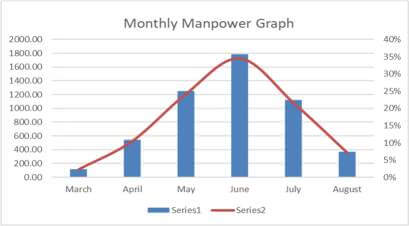
- Installation Material 90%
- Job Expense Material 78%
- Subcontractors 98%
- Installation Labor 98%
- Job Expense Labor 75%
- Overall budget used 91%
The end result was a 96% increase over the original estimated profit. The project also was completed on time with a satisfied general contractor and owner.
Safety
Safety was really put first on this project. With George McKenna’s dedication to safety along with Cadence McShane project team that took safety very seriously, we were able to complete many hazardous tasks with only one minor hand cut. Dealing with an existing school that had to stay in operation during construction there were several service shutdowns, re-energized existing electric rooms fed from the newly installed main switchgear, some decades old that without proper planning and MOP’s could have been very hazardous. All the work took place in a small area of the campus while 2793 students were in classes until summer freed up some working space. The addition was a two-story steel structure which had the added hazards of cranes and scaffolding. With the compressed schedule GME would have to coordinate working in areas alongside other trades, working long hours, and weekends. Constant attention to safety by our supervision, the general contractor, and other trades made this project a safe and productive project.